how to measure sheet metal parts Method of using a steel ruler. a) Measure length. b) Measure thread pitch. c) Measure width. d) Measure internal diameter. e) Measure depth. f) Draw lines. Directly measuring the diameter size (shaft or hole) of a part with a steel .
Full-service metal fabrication (also known as turnkey metal fabrication) utilizes a variety of equipment to innovate and improve products for our customers in an efficient and .
0 · wire gauge vs sheet metal
1 · standard thicknesses of sheet metal
2 · standard thickness of sheet metal
3 · standard size of sheet metal
4 · sheet metal specifications chart
5 · sheet metal size chart
6 · galvanized sheet size chart
7 · 20 gauge sheet metal dimensions
Tupperware Lunch-It Portion & Go Compact 2-Lunch Box Set - Dishwasher Safe & BPA Free - (2.3 Cups/550 ml)
In this video, you will see me explaining the basic steps required to measure and mark out on sheet metal in. These steps are transferable through any sheet . How to Measure Sheet Metal Thickness? There are two ways to measure sheet metal: using a measuring tape (which is less precise) and a .
Visual inspections—The most basic form of inspection, it involves inspectors examining the sheet metal parts for any visible defects, such as .
To find out the actual thickness of sheet metal, you can refer to a gauge conversion chart. This chart helps translate gauge numbers, such as 18 gauge, into familiar .This page uses sheet metal working as an example of metal working to explain basic knowledge of bending radius, how to calculate it, countermeasures to defects, problems in conventional bending radius measurement, and the latest . Method of using a steel ruler. a) Measure length. b) Measure thread pitch. c) Measure width. d) Measure internal diameter. e) Measure depth. f) Draw lines. Directly measuring the diameter size (shaft or hole) of a part with a steel .
If you need to measure sheet metal parts, it’s crucial to know how to convert measurements from one unit to another. There are three common ways to measure sheet .
Here’s a general guide on how to inspect sheet metal parts: Visual Inspection: Surface Quality: Check for scratches, dents, or surface imperfections that may affect functionality or aesthetics. Dimensions: Verify dimensions such .
Inspecting sheet metal parts involves a combination of visual inspections, dimensional measurements, and non-destructive testing (NDT) methods. The goal is to ensure . A sheet metal gauge is a standard unit of measure used to determine the thickness of a metal sheet. The gauge number and thickness have an inverse relationship – the higher .
Steel rulers are used to measure the length dimensions of parts, but their measurement results are not very accurate. This is because the spacing between the markings on a steel ruler is 1mm, and the width of each marking . Mitutoyo Sheet Metal Micrometers are used to measure the thickness of sheet metal, paper, plastic, and rubber parts where a deep throat micrometer is required. News. September 17, 2024. Sheet metal stamping parts are thin, soft, and prone to deform, which is hard to measure. This requires careful handling to prevent damage and distortion during inspection. The customer used to clamp the stamping part .Critically they are also very poor at measuring the location of the edges in sheet metal parts, particularly on thinner gauge materials. This is a serious problem as sheet metal parts are primarily defined by their edges. In figure 3 we can see a laser projected onto a part.
wire gauge vs sheet metal
From the U.S.Is there an industry standard for measuring parts after a bend in a brake press? For example: if I have 1⁄8-in.-thick steel, the drawing states that the bend line is 1 in. from the edge, and the notes on the drawing say to bend down 90 degrees, what is the proper way to check the 1 in. after it is bent—inside the bend or outside, which includes the thickness .
standard thicknesses of sheet metal
When a sheet metal part is bent, it physically gets bigger. The final formed dimensions will be greater than the sum total of the outside dimensions of the part as shown on the print—unless some allowance for the bend is taken into account. Many will say material “grows” or “stretches” as it is bent in a press brake. Now that each laser feeds more parts to more downstream machines, strategic part identification and sorting has become more important than ever. Measure What You Have. You send a nest to the laser to be scheduled among that day’s job list. The parts are cut, sorted, then sent downstream or stored as work-in-process (WIP) inventory. Surface Finish Scales for Sheet Metal Fabricated Parts. There are several different ways to measure the surface finishes of sheet metal fabricated parts. Fabricators, machinists, and metal finishers often use the highly technical Ra (Roughness Average) scale, which measures the average surface heights and depths across a surface. The problem is . To provide metalformers with a reliable and dependable process to instantly and accurately measure lubricant thickness, and to determine its distribution across the complete coil or sheet surface, Amepa GmbH (Amepa America Inc., Middleburg Heights, OH) has introduced an oil-film measurement (OFM) system.
These software provide sheet metal modules or related functions that can help designers with the design and unfolding calculations of sheet metal parts. Use the sheet metal module or tools in the software: Most 3D CAD software provides related tools and functions for sheet metal design. For example, Creo offers a variety of methods for .
However, often times sheet metal parts or rubber parts are difficult to inspect in their free state. If left to be inspected in their free state, these parts would likely deform due to gravity and distort under their own weight. The deformation would likely cause these parts to fail inspections of size, location, orientation, and form.The parts quoted were two bend sheet metal channels with holes in the top for slugs to weld to. Two parts needed to align together but overall channel dimensions has a bit of forgiveness in fit. Hole dimensions given from the final bent part.
If you need to measure sheet metal parts, it's crucial to know how to convert measurements from one unit to another. There are three common ways to measure Email: [email protected]
This whitepaper helps describe a set of broad guidelines that you can use while specifying tolerances for your sheet metal parts drawing(s). Essentially, these are in place due to practical limitations of sheet metal forming, shearing and punching. . The dimensional callouts display the measurement and the table below provides the tolerance . If you need to measure sheet metal parts, it's crucial to know how to convert measurements from one unit to another. There are three common ways to measure. E . Flatten your sheet metal part in SOLIDWORKS, expand the cut list on your Feature Tree, right click the sheet metal item, and select properties. How much mate.
Capturing accurate and detailed 3D measurement data on extremely large parts and assemblies is often a huge challenge. Conventional Laser Trackers, even with 6DoF, cannot see around large corners. Portable Measurement Arms .Bending radius is often used in sheet metal working. This page explains the working methods, measurement problems, and how to measure 3D shapes accurately. . In all, this method involves many problems; not all workplace operators can accurately measure profiles and not all parts can be measured. Along with that, some samples will need to be .
stainless steel lunch bento box
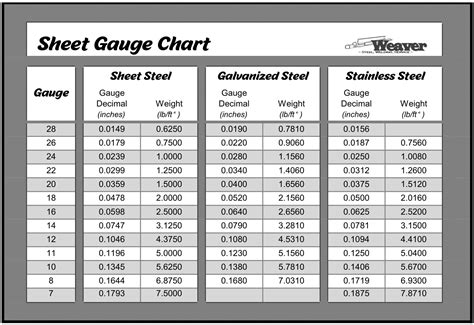
Here’s a helpful summary of the most common finishes for sheet metal. 6. Selecting the Wrong Sheet Metal for the Job. Imagine making hundreds of parts out of unfinished steel that are destined for installation in a salty, marine environment. Amazingly, .
stainless steel litter box with lid
Manufacturing sheet metal parts can be particularly difficult. The production cost per component is very low compared with other industries such as metal machining. This drives down the resources available to the quality control process, even though sheet metal parts are often used in the most demanding applications such as aerospace or automotive or in very large production runs, all . Manually calculate the K-Factor using the measure of sample sheet metal parts that were bent using the following formula: Note: Bend allowance is part between initial flat patter length of desired edges (arc length of the neutral axis through the bend):
Gillespie recounts how one researcher was able to construct a similar dial indicator gage for measuring a stack of five sheet metal parts. "The overall height of five parts was the total of the part thickness plus the burr heights," he says. He points out that the technique assumes a flat surface and no bowing induced by the preceding stamping . For very tight tolerances, heat expansion results in either metal parts failing inspection or, more commonly, a customer and supplier coming up with different measurements for the same part. . Utilizing a controlled environment helps to minimize the effects of heat expansion .
Try a cylindrical probe and not use edge points on sheet metal parts? Whoever employs you will likely jump at the chance to speed things up and save money. . instead use a VECTOR (or surface) point on the surface next to where you want to measure the edge, and measure the edge point relative to that point. ALL data for an edge point comes . Call the starting thickness of your sheet metal “S” and call the formed thickness of your part at the location of interest “F”. The percent thinning is calculated as T% = 100 * (S-F)/S. This is the actual percentage of material loss in a specific stressed area on your formed part. Common Standards for Dimensional tolerances. We adhere to various standards in sheet metal fabrication. ISO 2768 is the most widely used standard for general tolerances, while ANSI Y14.5 is more specific. These standards serve as a guide to ensure consistency in production regardless of the project’s complexity.. It’s not just about compliance; it’s about . Measuring Tolerance Representation Accuracy is critical in sheet metal fabrication drawings, to ensure that fabricated parts meet design specifications and fit together correctly during assembly. Sheet metal tolerances refer to the maximum permissible deviation range in the dimensions during sheet metal processing.
standard thickness of sheet metal
Twin Spindle Lathes. Twin spindle turning machines are advanced CNC machines designed to perform multiple operations accurately and quickly. These machines are specifically designed .
how to measure sheet metal parts|standard thicknesses of sheet metal